-
最近の投稿
アーカイブ
カテゴリー
投稿日カレンダー
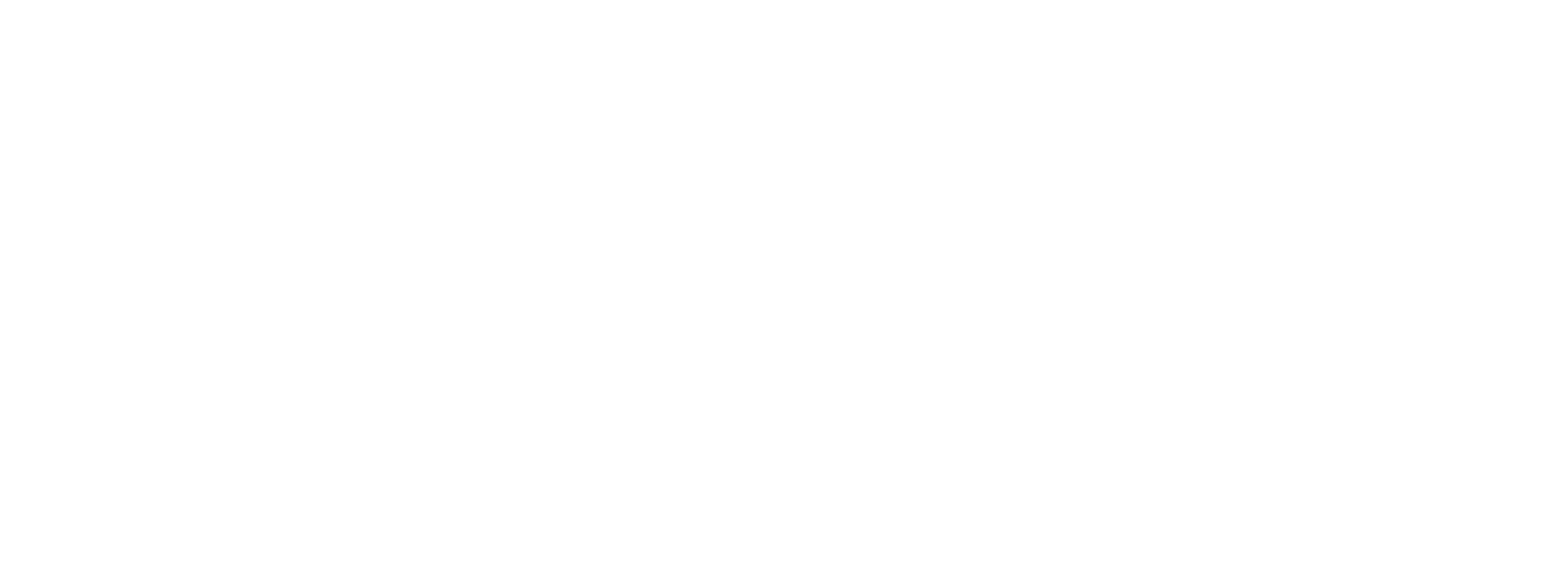
皆さんこんにちは!
株式会社ツバサオートメーション、更新担当の中西です。
本日は第8回制御盤設計雑学講座!
さて今回は
~鉄則~
ということで、制御盤設計における鉄則を詳しく解説し、プロフェッショナルな設計者が守るべきポイントを深く掘り下げます♪
制御盤は、工場・プラント・発電所・インフラ設備などで機械やシステムを制御するための重要な装置です。適切に設計された制御盤は、機器の安定動作・作業の効率化・メンテナンス性の向上・安全確保を実現します。しかし、制御盤の設計を誤ると、機械の誤動作・火災・感電事故・システムダウンなど、重大なトラブルにつながる可能性があります。
制御盤を設計する際には、以下の3つの基本方針を常に意識することが重要です。
安全性(Safety)
機能性(Functionality)
メンテナンス性(Maintainability)
制御盤内部の配置設計は、発熱・配線の取り回し・メンテナンスのしやすさを考慮して行う必要があります。
🔹 発熱対策
🔹 配線ルートの確保
🔹 メンテナンス性の確保
制御盤に供給される電源は、機器の種類や使用環境に応じて最適に設計する必要があります。
🔹 電源の基本設計
🔹 過電流・短絡対策
工場やプラントでは、インバーター・モーター・高圧機器などが発生する電磁ノイズが制御盤に悪影響を与えることがあります。ノイズ対策を怠ると、誤動作や信号異常が発生するため、しっかり対策を講じることが重要です。
🔹 ノイズ対策の基本
制御盤は長期間使用する設備であるため、メンテナンスのしやすさが非常に重要です。
🔹 保守性を向上させる工夫
近年、IoT・AI・クラウド技術を活用した制御盤が増えています。これらの技術を導入することで、効率的な運用やトラブル予測が可能になります。
🔹 最新技術の活用ポイント
制御盤設計における鉄則を守ることで、安全で効率的なシステムを構築することができます。
最新技術を活用しながらも、基本的な設計ルールを守ることが、信頼性の高い制御盤を作る鍵となります。
株式会社ツバサオートメーションでは、一緒に働いてくださる仲間を募集中です!
私たちが採用において最も大切にしているのは、「人柄」です。
ぜひ求人情報ページをご覧ください。皆さまのご応募を心よりお待ちしております!
皆さんこんにちは!
株式会社ツバサオートメーション、更新担当の中西です。
本日は第7回制御盤設計雑学講座!
さて今回は
~歴史~
ということで、制御盤設計の歴史と背景について深く掘り下げ、その進化が産業技術にどのような影響を与えてきたのかを解説します♪
制御盤は、電気設備や機械の動作を管理・制御するための装置であり、産業界において不可欠な存在です。歴史的には、手動スイッチから始まり、リレー制御、PLC(プログラマブルロジックコントローラ)、そしてIoT・AI技術を活用したスマート制御へと進化してきました。
制御盤の歴史は、19世紀後半の電気技術の発展とともに始まりました。それまでの工場の機械制御は、蒸気エンジンや水力を利用したベルト駆動システムが主流でしたが、電気が導入されることで、より精密な制御が可能になりました。
20世紀初頭には、電磁リレーを利用した制御システムが登場しました。リレーは、電気信号のON/OFFを制御するスイッチとして機能し、産業機械の自動化を促進しました。
この時期の制御盤は、大量のリレーを用いて機械の動作を順番に制御するものであり、回路設計が複雑になると配線ミスやトラブルが増えるという課題もありました。
1960年代になると、リレー制御の複雑化によるメンテナンスの手間や誤作動のリスクが問題視されるようになりました。この課題を解決するために、電子回路を活用した制御装置が開発されました。
PLCの特徴は、プログラムによる制御の変更が可能なことです。リレー制御では回路を変更するたびに配線を組み替える必要がありましたが、PLCならソフトウェアを書き換えるだけで制御内容を変更できるため、製造業の生産ラインの柔軟性が飛躍的に向上しました。
1980年代になると、PLCの処理能力が向上し、アナログ信号の処理やセンサーとの連携が可能になりました。これにより、温度・圧力・流量などの制御もPLCで行えるようになり、火力発電所・石油化学プラント・自動車工場などの大規模システムにも導入されるようになりました。
1990年代には、制御システムがさらに進化し、PLCとコンピュータを連携させたSCADA(Supervisory Control And Data Acquisition)が登場しました。
2000年代に入ると、PLC同士や上位システムとの通信にEthernet(イーサネット)が導入され、制御盤のネットワーク化が加速しました。
これにより、大規模な発電所や化学プラントでは、遠隔地からのモニタリングや自動調整が可能になりました。
2010年代以降、IoT(モノのインターネット)技術が制御盤にも導入されるようになり、リアルタイムデータの活用が進んでいます。
現在では、AIとIoTを組み合わせたスマート制御盤が開発され、以下のような機能が実現されています。
制御盤設計は、手動操作→リレー制御→PLC→ネットワーク化→スマート制御という形で進化してきました。
今後も、AI・5G・クラウド技術と融合しながら、より高度な自動化と効率化を実現する制御盤の進化が期待されます。
株式会社ツバサオートメーションでは、一緒に働いてくださる仲間を募集中です!
私たちが採用において最も大切にしているのは、「人柄」です。
ぜひ求人情報ページをご覧ください。皆さまのご応募を心よりお待ちしております!